Our Blog
How RF Welding Solves Supply Chain Issues for Manufacturers
Share this Article:
What is RF Welding
Radio Frequency (RF) welding, also known as heat sealing, is a process used to bond thermoplastic materials by using high-frequency electromagnetic energy. This energy causes the molecules in the materials to move rapidly, generating internal heat that fuses the materials together when pressure is applied. The result is a clean, durable, and uniform seal that is both airtight and watertight.
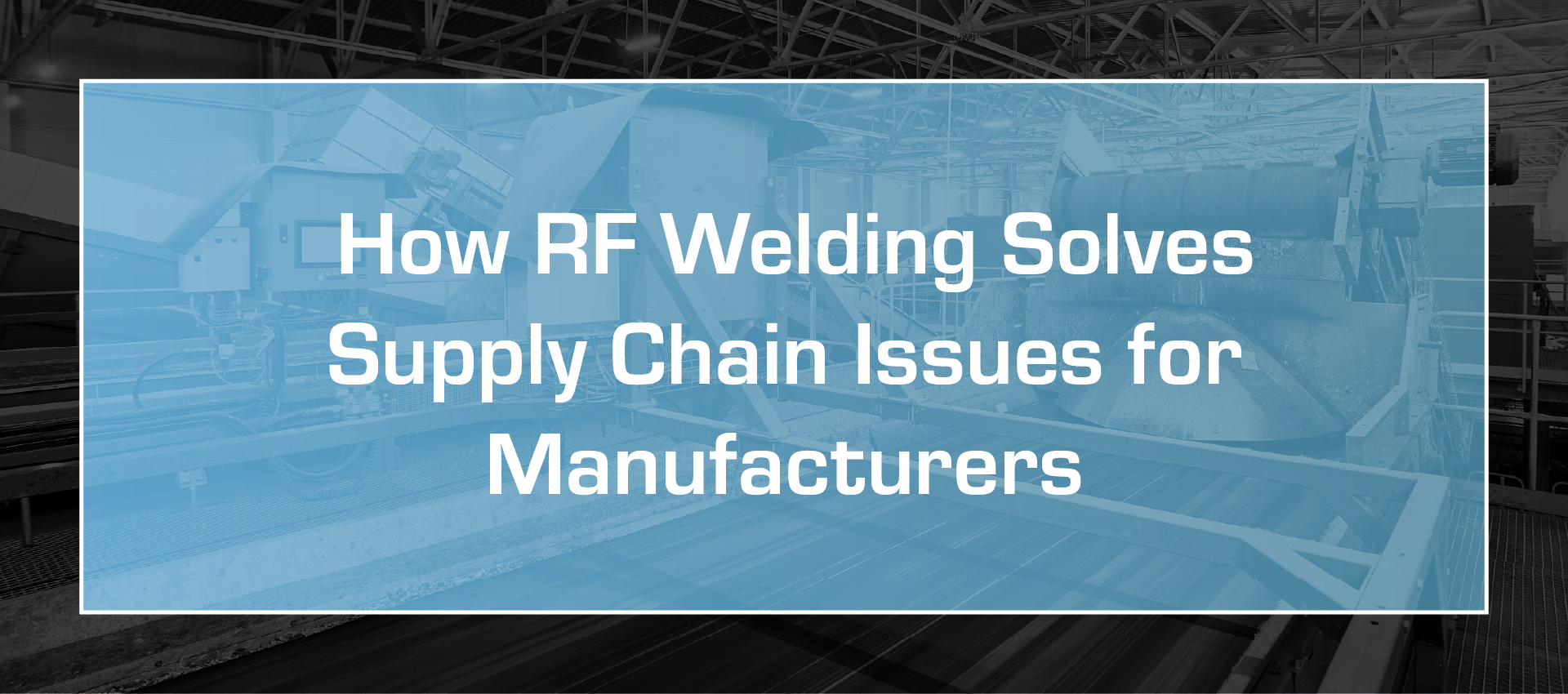
Unlike adhesives or stitching, RF welding creates bonds without additional fasteners or chemicals, reducing material complexity and eliminating many of the failure points that cause supply chain disruptions down the line. This makes RF welding an essential tool not only for high-performance manufacturing but also for mitigating common challenges in the production and distribution pipeline.
Reducing Material Waste Through RF Welding
One of the biggest contributors to supply chain inefficiencies is material waste, both from production errors and from poorly optimized design processes.
RF welding significantly reduces waste in several key ways:
-
Precision Welding
Because RF welding targets only the bonded area without damaging adjacent material, manufacturers experience far less scrap.
-
Tight Tolerances
The repeatable nature of RF welding allows for precise, automated processes that minimize human error and material misalignment.
-
Efficient Material Usage
RF welding is compatible with coated and flexible thermoplastics like PVC and TPU, which are often lighter and more durable, enabling thinner material profiles without compromising performance.
For manufacturers seeking to reduce costs and support sustainable production goals, less material waste translates directly into fewer supply chain interruptions, lower raw material orders, and improved overall efficiency.
Enhancing Product Durability to Minimize Returns and Replacements
Every product return, warranty claim, or field failure introduces additional stress on the supply chain, from increased reverse logistics to unplanned manufacturing adjustments. RF welding directly addresses this by producing more durable, reliable products.
- No Stitch Holes or Glues: RF welding eliminates traditional weak points in sewn or glued seams, resulting in longer product life.
- Stronger Bonds: The fused seams created through RF welding often exceed the strength of the original material, reducing the likelihood of seam failure during use.
- Environmental Resistance: RF welded seams hold up under extreme environmental conditions, from heavy rain and high UV exposure to chemicals and high-pressure loads.
For manufacturers in industries such as outdoor equipment, military gear, and industrial containment, this enhanced durability means fewer product failures and less demand on the supply chain for replacements or repairs.
Ensuring Consistent Quality for Predictable Output
Predictability is a key goal for any efficient supply chain. When production output is inconsistent, due to poor seam quality, manual labor variability, or inconsistent adhesives, manufacturers face unpredictable lead times, higher inspection rates, and inconsistent inventory quality.
RF welding helps prevent this through:
- Automated Consistency: RF welding machines are programmable for exact weld times, temperatures, and pressures, ensuring that each unit meets identical standards.
- Seam Repeatability: Unlike hand-sewn or glued products, RF welded seams are not reliant on operator skill, which eliminates variability across shifts and production runs.
- Scalability with Precision: Whether you're manufacturing 500 units or 50,000, RF welding scales easily without compromising quality.
This level of consistency supports lean manufacturing principles and streamlines the supply chain by reducing rework, minimizing quality control hold-ups, and improving customer satisfaction.
RF Welding as a Supply Chain Advantage
While many manufacturers focus on sourcing, shipping, and logistics to improve supply chains, the manufacturing process itself can be a powerful lever for optimization.
RF welding stands out as a strategic advantage for several reasons:
Fewer Inputs Required
Unlike sewing or gluing, RF welding requires only the core material and energy, reducing dependency on adhesives, thread, and other consumables that can be affected by global shortages.
Simplified Assembly
RF welded components often require fewer parts and steps, making the assembly process faster and more reliable.
Improved Inventory Control
With fewer sub-components and more durable finished goods, manufacturers can reduce stockpiling and emergency ordering.
Design Flexibility
The ability to weld flexible and rigid components allows for innovative designs that may consolidate multiple parts into a single, more efficient unit.
RF welding supports more efficient, predictable production by increasing in-house control, reducing reliance on secondary materials, and streamlining sourcing and assembly processes.
Partner with Carolina Covertech Today!
Carolina CoverTech is more than just a contract manufacturer–we are a supply chain solution partner for companies that demand precision, consistency, and innovation. With decades of experience using RF welding to manufacture products that cover, protect, contain, and enclose, we help our partners overcome complex production challenges while strengthening their operational reliability.
Our North Augusta, SC facility offers:
- Custom RF welding solutions tailored to your product requirements
- Full product development support, from concept through final production
- Industrial sewing and rigid-to-flexible conversions for hybrid applications
- Flexible production volumes with short lead times and rigorous quality assurance
Carolina CoverTech can help you create supply chain-resilient solutions that support your growth and minimize downstream risk.
Key Takeaways
RF welding streamlines production, reduces supply chain risk, and delivers durable, high-quality results.
Carolina CoverTech offers expert RF welding, flexible production, and engineering support to help you stay ahead in a challenging manufacturing landscape.
Let’s build smarter together!